On-Site Representation
MSCorp provides expert on-site representation for customers across the United States, from the East Coast to the West Coast and throughout the Gulf Coast region. Our staff is intimately familiar with all phases of shipbuilding, ship repair and ship modernization. When on-site, we are the “eyes and ears” for our customers. In a typical on-site representation scenario, we ensure all pertinent rules and regulations are not only understood but that they are being adhered to. We verify all deliverables are being built in accordance with specifications, and that the product will meet or exceed customer expectations. Additionally, to ensure the highest level of quality, we verify that components and parts have been tested and will not accept a product until it passes all requirements. We maintain a communication schedule that fits the customers needs to keep them adequately informed so they have the right information at the right time to make the best decisions to suit their needs. Our #1 priority is customer confidence and satisfaction!
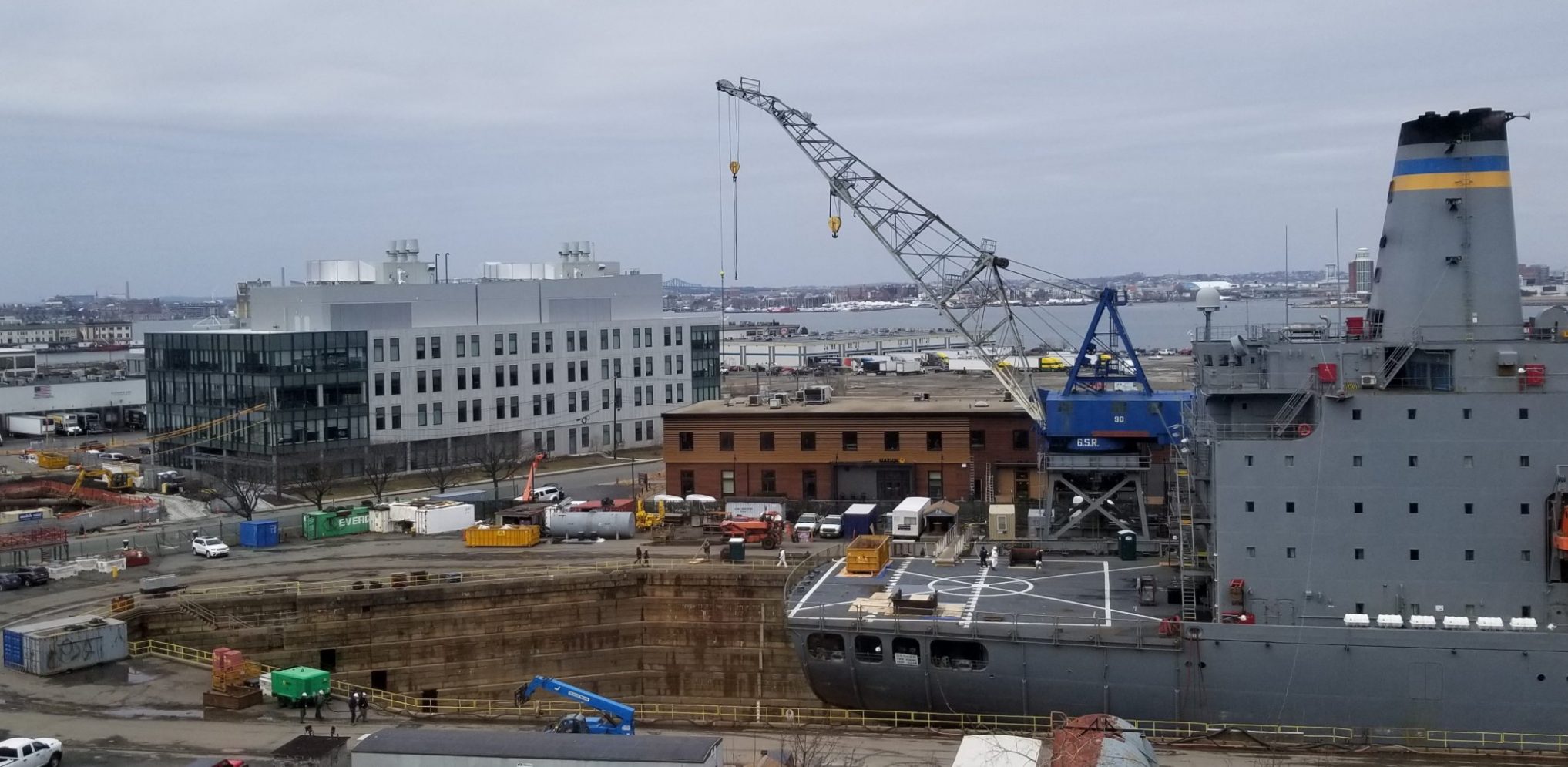
Commercial On-Site Representation Support
- Daily Job Log & Updates to Customer
- Daily Environmental Log (coating conditions)
- Communications Liaison among Customers / Shipyard / Naval Architects / Vendors / Regulatory Bodies
- Inspection Schedule Coordination with Shipyard and Regulators
- QA Inspection of:
- Equipment Installations;
- Welding; Coating Prep and Application;
- Tank and Piping Cleaning & Testing;
- Gas Freeing;
- Electrical Installations;
- Hazmat
- QA of vendor and shipyard material deliveries and document organization
- Job Progress and Cost Tracking
- Photographic record
- Document collection, indexing, filing
- Owner Furnished Equipment Tracking/Customs Clearing / Shipper Communications
- Change Order / Condition Report Processing
- Drawing Submittal Tracking
- As-Built Drawing Tracking
- Delivery Prep and Arrangements
- Officer & Crew Coordination
Government On-Site Representation Support
- Provide Subject Matter Expertise (SME) during meetings pertaining to craft / vessel scheduling, maintenance, configuration and emergent repairs
- Attend daily program production status meetings to assist the Regional Maintenance Centers (RMC) and contractors in problem resolution
- Draft Liaison Action Reports (LARs) against drawings to identify and correct discrepancies
- Monitor and report configuration changes to the Configuration Data Manager (CDM)
- Participate as an INSURV preparation inspection team member for craft delivered back to the Unit following major overhauls (e.g., SLEP). Specializations include:
- Hull,
- Mechanical,
- Damage Control, and
- Craft Pre-Mission Check Lists.
- Monitor and report on Craft Corrosion Control Inspections
- Manage the Weight and Stability program
- Provide HM&E Technical direction
- Participate in Pre-Overhaul Test and Inspection (POT&I)
- Provide direct support to the Advanced Planning Yard Manager with review, red line and updating all Work Specification Items (Work Spec’s) for contracted availabilities